1980 Original Building -- Passive Solar Design
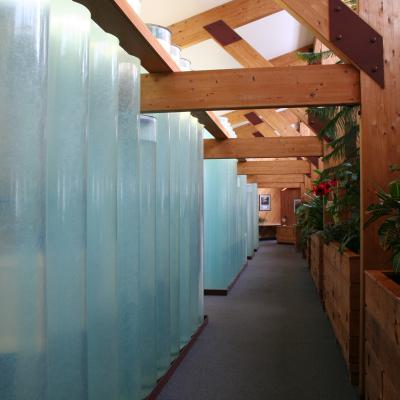
Regionally grown wood from New England’s forests are featured throughout the building. The laminated carrying beams are made from eastern red spruce. The staircases combine oak steps with cherry and pine railings. Much of the paneling is native eastern white pine, and the walls at the end of the corridor are paneled with butternut. This helps local and regional economies and helps to create and sustain jobs in New Hampshire and New England.
1990 Weeks Wing addition
In 1990, the Forest Society’s new addition was named for U.S. Senator John W. Weeks; sponsor of the Weeks Act in 1911 that established the National Forest system. The terrain east of the original Conservation Center building dictated placement of the Weeks Wing in a northeast exposure. This eliminated the possibility of substantial use of the sun for passive solar energy. Also, the growing number of personal computers at each desk and their associated heat gain made solar gain less critical. Other features include triple-glazed windows and transom windows above each office door for better air circulation. The roof has a “sugar house” clerestory design to maximize natural daylighting capabilities and to increase the summer air exhaust through electrically operated windows. A berm on the north side of the wing keeps the exterior part of those walls at 55 degrees in hot and cold weather. The Weeks Wing is enclosed in “Blown-in Blanket” (BIBs) insulation. By this method, insulation is blown into the cavity between the exterior wall sheathing and a mesh; on the inside resulting in the ability to see and fill missed areas. The Weeks Wing was built largely with local wood products such as white pine for clapboards, pine boards for sheathing, green hemlock for framing and white ash for interior wainscoting and trim.
2001 French Wing addition – USGBC LEED-Gold® certified
This 11,400 square-foot wing was completed in April 2001 and was awarded the first LEED-Gold® certification in New England by the U.S. Green Building Council. Large pine trees harvested and milled on-site comprise the timber frame of this wing. The majority of the wood used for the building was harvested in New Hampshire. The red oak stairs, cherry and birch railings, ash trim, and red maple wainscoting were procured from working forests and timberland owners across the state.
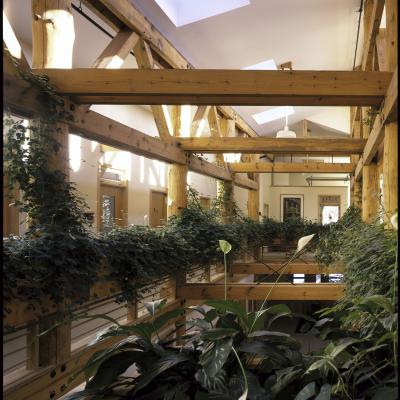
The French Wing’s air tight shell has seven inches of blown in cellulose insulation in the walls and fourteen inches of insulation in the ceiling made from recycled news print. This insulation provides resistance values of R-24 and R-42, respectively. It also prevents the accumulation of moisture in the walls, which has potential to create mold problems. To further ensure superior air quality, the Forest Society chose paints, finishes, and adhesives specifically for their low toxicity. Outside air is continuously brought in to each room, through an energy recovery ventilation system. The central copier is located in a separate room and is exhausted outside to avoid ozone and toner dust in the offices and common areas.
A significant amount of the French Wing was made from recycled materials. The tiles on the floor of the atrium are made from recycled aircraft window glass, and the handicap ramp outside is composite lumber made from recycled soda bottles and sawdust. The Durisol® foundation blocks are made from a combination of cement and recycled construction wood debris. Finally, a portion of the drywall and carpet in the building are reused too. During construction of the French Wing, rather than having all the debris go into one dumpster, there were bins to sort out almost every kind of material- metal, wood, plastic, non-recyclables, etc… Approximately 90% of the construction waste was recycled.
Planters surrounding the atrium are watered using filtered water from the sinks, a water fountain, the shower, and the dishwasher. This “greywater” is captured, filtered and then pumped back up to the planters. The water not used by the planters then drains to a secondary tank that waters a flower bed on the south side of the building. There are two sets of composting toilets in the building. First there are two foam flush toilets manufactured by Clivus New England upstairs here on the north side of the building. Each uses about two ounces of water per flush. There are also two flushless Phoenix model toilets which use no water. All the bathrooms are connected to basement composting units where human waste and toilet paper are mixed with wood shavings. Over time, this will decompose into valuable compost. Most modern-day toilets use over fifty times more water than the Clivus composting toilets. The French Wing uses approximately 20 gallons of water per day – that’s almost 90% less water than an office building of similar size and occupancy.
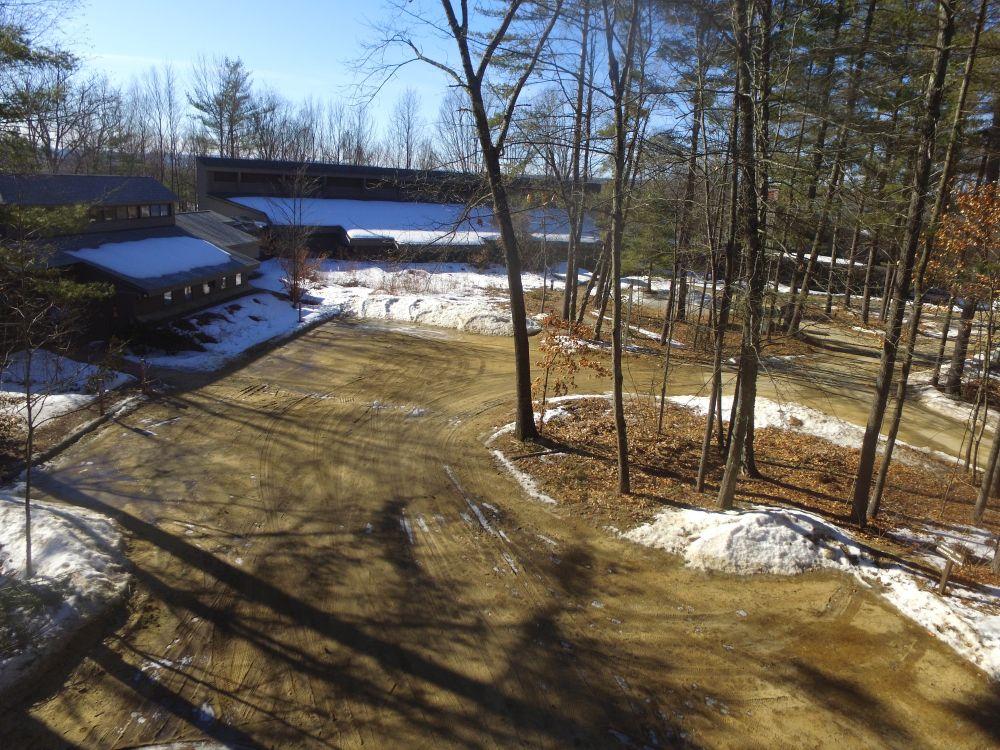